Post updated on August 10, 2024.
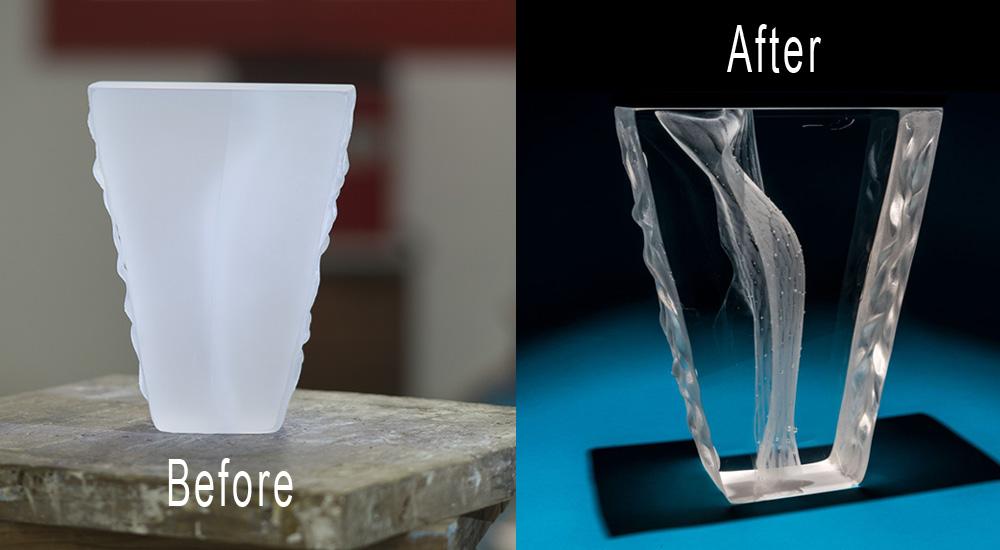
Polishing glass, especially optical glass, is a crucial step in the glass sculpting process. After firing the glass sculpture in the kiln, the next challenge is to polish it to achieve optical transparency. The process requires patience and precision.
The polishing process
Polishing optical glass involves multiple grinding and polishing stages. I use a vibrating lap machine with silicon carbide abrasive and water, which takes longer than other methods like diamond discs. For a 5-sided piece, the polishing process can take up to 100 hours, with 20 hours spent on each side.
Grinding & pre-polishing steps
The grinding process starts with coarser grits and progresses to finer grits:
- 80-120 grit (rough grind): 3 hours
- 220 grit (semi-smooth): 3 hours
- 400 grit (smooth grind): 4 hours
- 600 grit (super smooth): 4 hours
The process starts with 80 or 120 grit (depending on how much glass you want to remove) and goes up to 220, 400, and 600. At each stage, I thoroughly clean the plate to ensure no previous grit remains on the surface. Microparticles from previous grits can cause scratches, so cleaning is critical.
Grinding tips
- Add 3-4 tablespoons of silicon carbide abrasive to the plate, and at the 600 grit stage, include a bit of soap to reduce surface tension.
- Mark each side of the sculpture with permanent marker lines to ensure even grinding. Technically, when all the marks are gone, the piece is ready for the next stage.
- Add fresh grit every hour.
- Clean the plate thoroughly when switching between grits to avoid cross-contamination.
- Use less water with finer grits to prevent the glass from moving without grinding.
Safety Tip: Always wear an FFP3 mask to protect your lungs from harmful dust particles released during grinding and polishing.
Final step: polishing
After completing the grinding and pre-polishing stages, thoroughly clean the disc and bumper ring. Make sure there are no particles of previous grit left behind.
Place the felt polish pad on the surface. Mix cerium oxide with distilled water until you obtain a slurry paste. The consistency should be like heavy cream.
Slowly pour the mix until a light surface of polish slurry covers the pad. Avoid excess water, as this will needlessly slow down the polishing time.
Average polishing time:
- Cerium oxide (polishing stage): 4–8 hours.
Polishing glass tips
- Always inspect the sculpture for leftover grit before beginning the polishing phase.
- Use a protection ring to prevent cerium oxide from splashing.
- Wear gloves and an FFP3 mask when handling cerium oxide.
- Keep a close eye on the sculpture to avoid overheating during polishing.
Avoiding scratches during polishing
One of the most challenging aspects of polishing glass is ensuring that no scratches form on the surface. Scratches happen when previous grit particles remain on the disc, causing damage during the polishing stage. Proper disc cleaning between each grit stage is essential.
The cleaning process for polishing glass
The disc must be cleaned thoroughly using a high-pressure water gun and a brush to remove all previous grit before moving to the next polishing phase. This meticulous process helps achieve the flawless, transparent finish essential for optical glass sculptures.
This video shows the process of cleaning the disc to ensure no previous grit is left on the surface. It is a tedious process—you need to take the disc outside every time and use a high-pressure water gun and a brush.